At the risk of oversimplifying, let me borrow a metaphor we can all relate to: baking cookies. At...
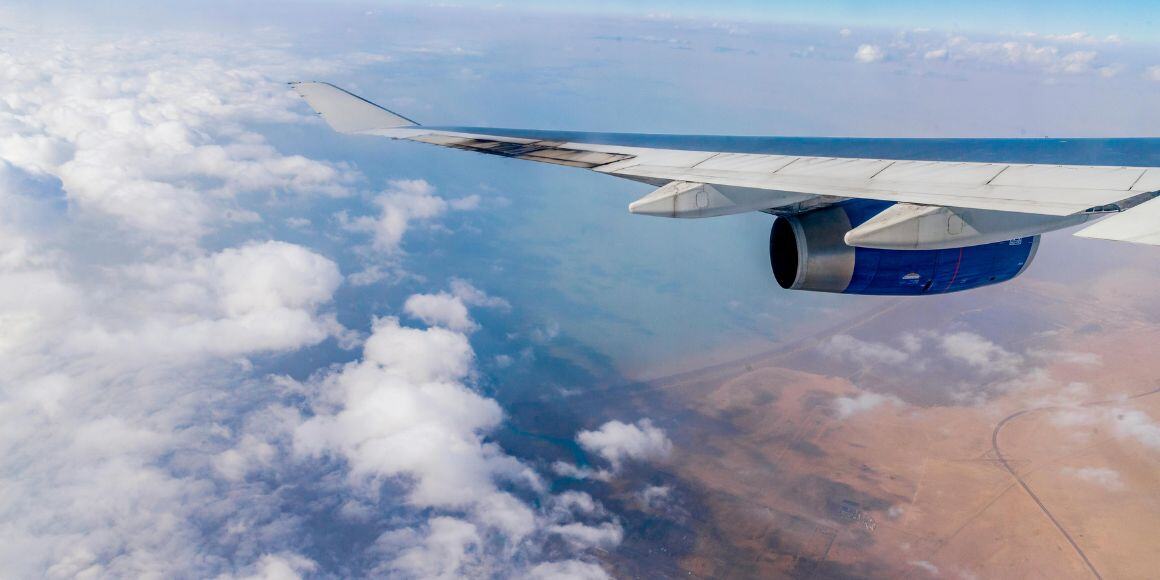
How High-Performance Investment Casting Filters Revolutionize Aerospace Manufacturing
Precision is the cornerstone of aerospace manufacturing. Each component, whether in a jet engine or a structural part, must meet rigorous safety, reliability, and performance standards. Yet, achieving such precision is no small feat. Investment casting—a centuries-old method—presents challenges ranging from controlling molten metal flow to reducing costly defects in the aerospace industry.
High-performance molten metal filters are revolutionizing this process. By addressing industry pain points and enhancing manufacturing outcomes, these investment casting filters redefine what’s possible in aerospace. Here’s how.
The Challenges of Investment Casting in Aerospace Manufacturing
Aerospace manufacturing relies on three primary types of castings, each with its unique requirements:
- Equiaxed Grain Castings: These castings are used for the cooler parts of jet engines. They require quick pouring to avoid voids or inclusions.
- Directionally Solidified Castings: Grain alignment is controlled to increase creep resistance for parts exposed to extreme heat. The challenge here is to withdraw the alloy while it is still molten, which demands very controlled pouring conditions.
- Single-Crystal Castings: This is mind-blowing technology (at a mind-blowing cost!). These advanced castings are made from a single grain, offering unparalleled performance but demanding exceptional precision and consistency.
Across the three types of casting processes, costs are consistently high due to several factors. The primary drivers include the time-intensive nature of investment casting and the expense of the alloys used.
For example, single-crystal alloys are known for their great performance and cost. They can cost up to $1 million for 5,000 pounds.
Additionally, the complexity of the process, with numerous steps and the need for highly specialized engineers, contributes to the high costs. This is why cost reduction becomes essential to ensure efficiency without compromising quality.
How High-Performance Filters Transform the Process
1. Improving Molten Metal Flow
Enhancing the flow of your alloy requires striking the right balance between speed and consistency, depending on your casting goals. For equiaxed grain castings, speed is crucial to ensure smooth pouring, prevent non-fills, and avoid splashing—ultimately reducing rework and scrap.
On the other hand, directionally solidified castings demand steady, controlled flow to achieve precise grain alignment and maintain structural integrity.
Holy Filters deliver on both fronts. They allow for faster, defect-free pouring while also ensuring consistent, reliable flow rates. With their advanced design, these investment casting filters help you achieve superior casting quality and operational efficiency.
2. Enhancing Filtration Efficiency
Traditional foam filters often fall short due to their inconsistent flow rates. Even the best foam filters may include scrap if not cleaned properly.
Applied Ceramics’ straight-channel ceramic filters offer 100% surface interaction, capturing debris and slag more effectively. Additionally, their ceramic composition adheres to dross, removing harmful inclusions and improving alloy purity. In simple terms: our Holy Filters require no cleaning.
3. Minimizing Scrap and Rework
Investment casting is costly not just because of all the steps it takes, but all the high-specialty engineers you need to make it right. High-performance filters reduce scrap rates and rework by eliminating defects like inclusion scrap and voids.
Manufacturers report yield improvements of 6-12% compared to foam filters, with potential increases up to 20% for processes previously lacking filters.
The Role of Filters in Aerospace Quality Assurance
Designated Quality Representatives are employed by the vendor but trained by the end customer to ensure all specifications are met. They hold the authority to approve or reject a production batch, and their decision is final. Even the plant manager cannot override their judgment, making them critical gatekeepers for quality assurance in the aerospace industry.
While inspection methods improve, specifications become tougher. This is why it’s essential to be armed with the right technologies and ensure quality throughout your production.
High-performance filters help manufacturers comply with stringent industry standards by:
- Reducing Castings Defects: Reliable filtration processes reduce inclusions, voids, and slag.
- Maintaining Consistent Quality: Filters support steady flow rates, crucial for meeting exacting aerospace manufacturing standards.
- Reducing Inspection Failures: With advanced filtration, aerospace manufacturers face fewer rejections during quality control.
By delivering cleaner castings with fewer defects, Applied Ceramics’ filters give engineers the confidence to meet—and exceed—the industry’s demands.
Success Stories: Filters in Action
One of our clients experienced transformative results after switching from foam filters to Holy Filters. They saw:
- 12% Yield Improvements: Reduced defects and inclusion scrap increased overall efficiency.
- Cost Savings: Eliminated the need for frequent rework, saving time and resources.
- Enhanced Quality: Produced components that consistently passed rigorous inspections, strengthening customer trust.
These real-world outcomes demonstrate the tangible benefits of investing in advanced filtration technology.
The Future of Investment Casting in Aerospace
As aerospace specifications grow stricter and inspection methods become more sophisticated, manufacturers must adapt to meet these evolving standards. Engineers are beginning to question the effectiveness of foam filters, as their contribution to inclusion scrap has raised concerns. Trials with ceramic filters, such as those developed by Applied Ceramics, have allowed aerospace engineers to uncover unique results. These advanced materials offer superior performance at a competitive cost, making them an increasingly attractive choice for many foundries.
As an industry partner, we always look forward to participating in trials and partnerships to develop even better materials and filtration techniques, ensuring the industry continues to advance.
High-performance molten metal filters are more than just a tool—they’re a catalyst for innovation in aerospace quality assurance. By improving flow, enhancing filtration, and reducing defects, these filters empower manufacturers to produce components that meet the highest standards of precision and reliability.
As the aerospace industry explores new possibilities, tools like these filters will continue playing a critical role.
Ready to transform your casting process?
Contact Applied Ceramics today and discover how our molten metal filters can elevate your manufacturing capabilities.