Reduced Scrap.
Less Reworks.
Higher Performance.
More Value.
Since 1984, Applied Ceramics has partnered with Aerospace engineers & other investment casting businesses to deliver superior metal filtration products.
Learn how our molten metal filters lower investment casting costs while contributing to a superior final product ⤵️
Why Leaders in the Investment Casting Industry Choose Applied Ceramics
EXPERIENCE THE ADVANTAGES OF LAMINAR FLOW
-
Enhanced Quality
Our ceramic honeycomb filters induce laminar flow, ensuring superior removal of debris, slag, and inclusions from molten metal.
-
Improved Flow Stability
Enjoy stable and fast molten metal flow, preventing oxidation, splashing, and air ingress for higher-quality castings.
-
Consistency
Unlike foam filters, ceramic honeycomb filters offer consistent flow rates, minimizing variability and ensuring reliable solidification control during casting.
-
Reduced Splashing
Laminar flow minimizes the 'splash' effect, enhancing casting integrity and reducing void inclusions for superior final products.
-
Enhanced Control
Benefit from precise flow control and minimized flow variations, ensuring consistent casting quality from pour to pour.
MOLTEN METAL FILTERS
Applied Ceramics has manufactured ceramic honeycomb filters for metal filtration in its USA facility since 1984.
In the casting of high-temperature liquid metal, ceramic honeycomb improves casting quality and consistency by:
filtering out impurities
- Reducing splash
- Optimizing flow rates
- Reducing casting porosity
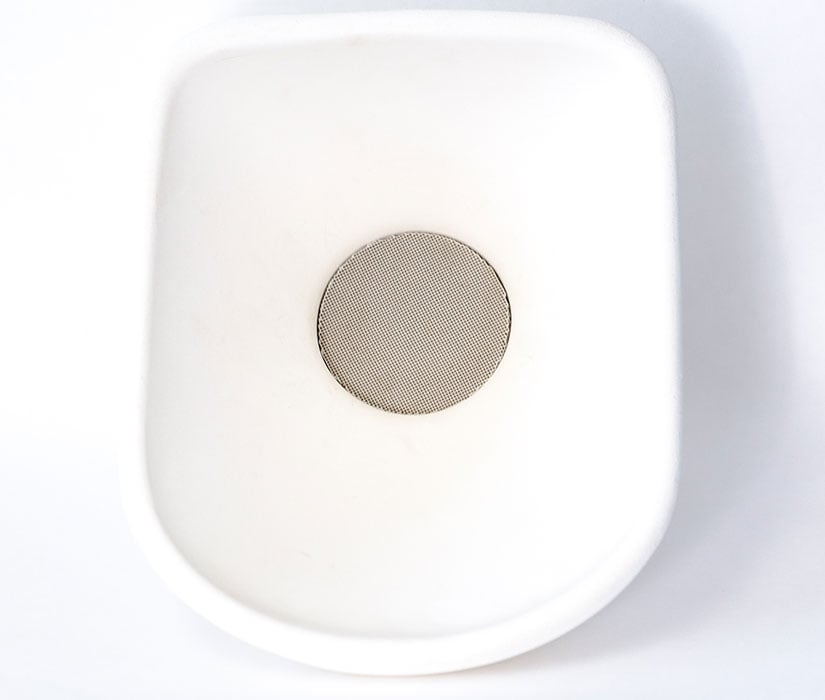
“It is not enough for a filter to just have good filtration efficiency. It must also have a high and consistent flow rate, good strength, a high capacity and good dimensional accuracy. This must be achieved at the lowest possible cost. Some of these parameters are in conflict with each other, for example if a filter has a very large capacity, the filtration efficiency may be compromised. The most effective filters are therefore ones that have been engineered to give the optimum performance over all of these parameters.” – Industry Expert
Filter Sizes Available
Don’t See what you’re looking for? Talk to our Sales team to learn more about our custom sizes & shapes available.
Typical Sizes | Minimum | Maximum |
Length or Diameter (in) | .75 | 6.50 |
Width (in) | .75 | 6.50 |
Height (in) | .25 | 12 |
CPSI | 4 | 500 |
MATERIAL PROPERTIES
Properties | Values |
Mullite Content | > 85% |
Amorphous Phases | < 15% |
Coefficient of Thermal Expansion | 5.1 x 10-6in/in°C |
Resistance to Thermal Shock | Excellent |
AI2O3 | 0.554 |
SiO2 | 0.424 |
K2O | 0.0015 |
Na2O | 0.0005 |
TiO2 | 0.0112 |
CaO | 0.0005 |
Fe2O3 | 0.0043 |
MgO | 0.0005 |
Pb | <10 ppm |
Bi | <0.5 ppm |
Ag | <10 ppm |
Sb | <5 ppm |
Zn | 45 ppm |
Sn | 5 ppm |
ACI Affiliations
ISO 9001:2015 specifies requirements for a quality management system where an organization:
- Needs to demonstrate its ability to consistently provide product that meets customer and applicable statutory and regulatory requirements, and
- Aims to enhance customer satisfaction through the effective application of the system, including processes for continual improvement of the system and the assurance of conformity to customer and applicable statutory and regulatory requirements.
THROUGH THE YEARS
Applied Ceramics (ACI) begins in Atlanta, GA at the present site. ACI provides alumina kiln furniture to 3M-Alsimag, General Electric, Kemet, AVX and other ceramic companies mostly as saggers and plates.
Diversified into the Electronics industry using Zirconia material. Focuses heavily on Barium Titanate Capacitor Industry and supplies all domestic users within the next two years.
Strategic decision to bring on R&D department head and a focus on innovating new products. Mostly materials development leads to multiple formulas and product knowledge for kiln furniture markets. ACI also begins partnering with larger companies to develop and sell new products.
As a part of the strategy to look for new markets, ACI acquires the base technology for the manufacture of ceramic honeycomb, Versagrid™. While these products were originally intended for the kiln furniture industry, it led to many more opportunities. Currently used in the environmental industry, ceramic honeycomb now supports other industries as well such as molten metal filters, mechanical and/or thermal supports and gas or liquid flow control.
ACI begins manufacturing its Firecat™ ceramic honeycomb and supplying the wood burning stove industry. ACI is the only US manufacturer of ceramic wood burning stove products and produces and services all products in both ceramic and metal.
ACI enterers into a venture with the Hyundai group of Korea to produce ceramic honeycomb for the environmental industry. ACI establishes and staffs a Contract R&D team to assist customers with innovative solutions.
ACI enters into a joint venture with General Motors to produce automotive substrates internationally.
ACI acquires United Emissions Catalyst and its catalytic coating capability.
ACI purchases Fisk Tool and its canning capability.
ACI purchases Amazon Ceramics to expand its product offering and its technical ceramic processing knowledge.
ACI purchases another manufacturing facility with a tool shop, expanded laboratory and test facility in Laurens, SC. ACI also operates a full service tool & die shop and laboratory that supports both locations, its ventures and its respective customers.
ACI absorbs NRG Ceramics under an agreement after private labeling products for NRG in the Aerospace and Defense industries since 1984.
QUESTION AND ANSWER SESSION
In the discussion of molten metal filters several issues must be resolved. First is the mechanism of filtration. There are three types of filtration mentioned in literature and in our understanding.
The first is sieve technology. This is as obviously as its name. It is a simple accounting of the diameter of particulate not being able to pass through the diameter of the holes doing the filtering.
The second technique is called filter cake. This is where a large particle is captured at the surface of the filter and then as a result of chemical actions adsorbs or attracts other particles of smaller size much the same as you would see with a filter cake.
One must consider the morphology of the particles being captured. For example, Hafnium Oxide has a ‘stringer’ morphology. Thus, one can use a cell size larger than the particle because the stringer will create a net on the surface of the filter to trap finer contamination.
The third technique is of the most interest to us. This is a boundary layer or stagnant layer that occurs above the filter. This layer exists between the region of turbulent flow of the metal being poured and the laminar flow created in the filter. The mechanism while not totally understood is well documented. Post mortem polished cross-sections clearly indicate this layer. It is believed that this stagnant layer captures small particulate holding it in place while the vast majority of the metal passes directly through in a laminar fashion into the molds. This laminar flow versus turbulent flow also will also reduce casting shrink and wall splatter inclusions.
A Honeycomb filter inserted in a pour cup will significantly reduce the macro shrink in the pour cup that pipes down into the casting runner system. This may eliminate ceramic contamination from a cutoff wheel and steel shot from the cleaning process that may get trapped in the shrink contaminating the revert. Placing a honeycomb filter in the tundish at the top of a master metal ingot will have the same effect on the shrink pipe in the bar.
One of the issues with foam filters and the often touted tortuous path, is back pressure. As a result, there are two issues that occur far too frequently. One is freeze off as the back pressure is too great and the other is bypass where the metal floats the foam filter and simply flows around it. These are not a known issue with the cellular honeycomb.
Hafnium Oxide contained in many DS alloys has a chemical affinity for aluminum oxide. This has been an accepted truth in investment casting for many years. Alumina balls could be put into the pour cup to grab the Hafnium Oxide. It works, but it is very expensive. Foundries had scrap out a pound of DS alloy with every pour. Replacing alumina balls with a Versagrid ceramic filter would be a significant cost savings.
One could also use a ceramic filter to hold the alumina balls out of the pour cup metal. The molten metal would pass over the aluminum balls, but would not be contained in the pour cup revert.
Sizing of the filter is as much art as science. The flow required is determined by the alloy, the temperature, the casting size and the specific casting process. As the manufacturer here is Atlanta, the filter diameter (square and rectangular are also available), thickness and size of the cells (cpsi) are all adjustable and can be readily sampled for trials. The material we use is a 30 year development effort to achieve a high strength, thermal shock resistant body that has many years of success and a multitude of satisfied customers.
ADVANTAGES OF ACI CERAMIC HONEYCOMB FILTERS
- In the aerospace and medical industries “cleanliness is next to godliness.”
- The primary performance indicator for a filter is that it CANNOT be a component that INTRODUCES foreign material into the casting.
- Customers consider things like dust, flakes, chips, etc to be bad news for their castings. When it comes to final inspection of finished goods, it is critical that product be cleaned prior to inspection and then directly segregated into a clean, controlled environment for final inspection and promptly sealed and packed afterward.
- All product specifications need to reflect this relative to the end users tolerance of inclusions in their castings
- Thermal shock tolerance is another big component. Filters are frequently preheated with the casting molds to 1700-2000°F, brought into ambient and then have molten metal poured into them. ACI’s L3MM blend has very high performance in this environment.
- Unlike zirconia which will phase transition when heated/cooled, ACI’s L3MM blend’s chemical properties are “locked in” during firing. Re-heating or pre-heating the L3MM filters has very little if any effect on the performance and structural characteristics of the material.
- Melting temperature of L3MM has been determined to be around 3200°F.
- Relative to foam filters, the honeycomb filters have the advantage of being able to be made thinner. This can often times allow for better pricing despite at higher cost/in3 of material.
- Ceramic honeycomb filters are used in the metallurgical and foundry industry due to is product features with large surface area, high mechanical strength, product consistency and excellent thermal shock resistance.
- With its unique straight channel honeycomb designs, it can increase the specific surface area between molten metal and ceramic filter. This improves its filtering ability to get rid of non-metal impurity and gas, purifying and making the metal liquid steady.
- As a result, it reduces the casting costs and improves the quality of the product. High grades of raw material and accurate processing make the quality of ceramic honeycomb filters extremely stable and consistent. Currently, ACI ceramic honeycomb filters have been applied to aerospace, automotive, machinery and many other casting areas, to improve the reliability of performance casting.
Enhance your investment casting production
We help engineers lower production costs through customizable and reliable innovation. Talk to our experts today about your project challenges to learn how we can help.