Precision in investment casting isn’t just a goal; it’s a necessity. Industry success –ranging from...
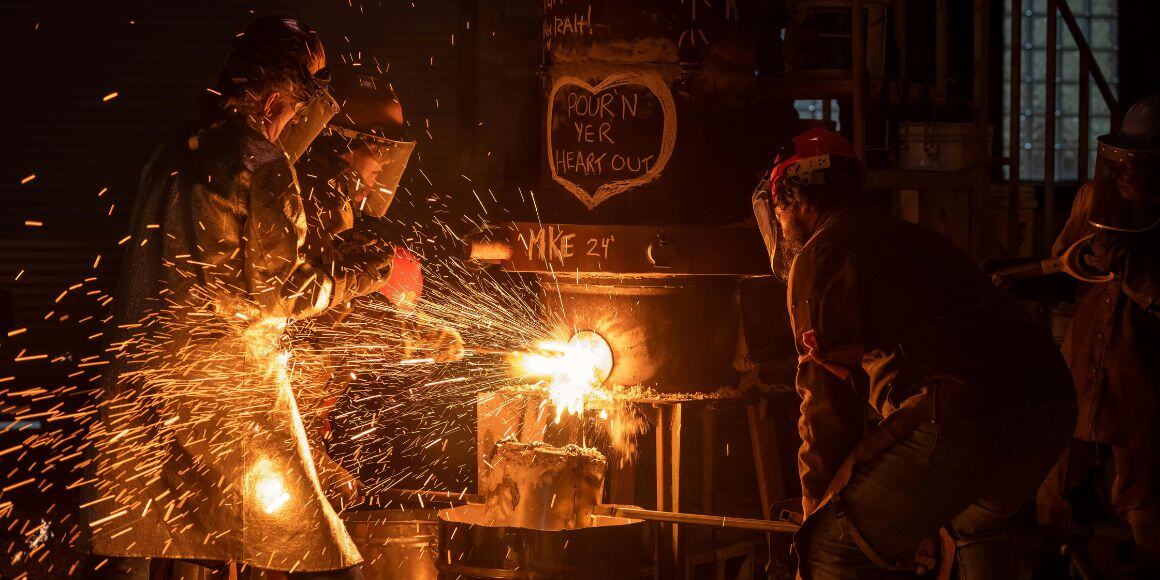
Key Benefits of Investment Casting Filters
- Improved Metal Purity – Filters remove oxides and inclusions for stronger, defect-free castings.
- Better Surface Finishing – Minimizes porosity and turbulence, reducing rework.
- Cost Reduction – Higher yields and fewer defects lower total processing costs.
- Thin-Walled Casting Optimization – Controlled flow prevents non-fill issues, which is crucial for aerospace and turbine blade applications.
Breaking Down the Cost of Investment Casting Filters
Choosing the right filter material and design for your investment casting process affects production efficiency and costs. Let’s explore their differences.
Traditional Foam Filters: Low Cost, High Risk
Foam filters are widely used due to their low initial cost. However, their performance limitations can lead to increased scrap rates, inconsistent flow, and inclusions in castings—all of which raise long-term processing costs.
- Initial Cost: $2–$5 per unit
- Filtration Efficiency: Moderate, but prone to breakage and residual debris
- Durability: Fragile; can introduce contaminants if not cleaned properly
Honeycomb Ceramic Filters: Balanced Cost and Performance
Applied Ceramics’ filters, particularly honeycomb designs, offer a balance between cost and efficiency. They provide laminar flow, improving metal purity and reducing defects.
- Initial Cost: $1–$4 per unit
- Filtration Efficiency: High; provides laminar flow. Highly customizable.
- Durability: Withstands extreme temperatures and requires no cleaning
3D-Printed Filters: Customization at a Cost
While 3D-printed filters offer precise customization, they are significantly more expensive and require longer production times, making them less viable for high-volume operations.
- Initial Cost: $6-$16 per unit
- Filtration Efficiency: Very high; highly customizable
- Durability: Reliable but cost-prohibitive for many foundries
When evaluating investment casting cost estimation, manufacturers must weigh filter cost against the potential savings from reduced defects, lower rework, and improved process efficiency.
Diagram showing the different filtration paths depending on the filter material. The Honeycomb design of Holy Filters™ allows for laminar flow, which helps speed up filtration and prevents splashing and inclusions.
What Else Affects the Investment Casting Cost?
Beyond filters, several key factors influence the total investment casting cost estimation:
- Material Costs: The cost of investment casting varies based on the metal alloy used. Among steel castings, high-grade stainless steel is the most expensive. Material costs in investment casting depend on the specific grade—for instance, SS316(L) is priced higher than SS304(L) due to its enhanced corrosion resistance and durability.
- Design Complexity: Intricate designs with tight tolerances require sophisticated molds and additional labor, increasing production costs. Simple designs without internal passageways or complex features equal lower expenses.
- Tooling and Mold Costs: Creating wax patterns and ceramic shells represents a substantial initial investment. Tooling costs can range from thousands to hundreds of thousands of dollars, depending on the part's complexity.
- Production Volume: Higher production volumes can distribute the fixed tooling costs over more parts, reducing the per-unit cost. Conversely, low production volumes may result in higher per-unit costs due to the significant initial tooling investment.
- Labor Costs: The labor involved in the investment casting process, including mold creation, casting, and finishing, contributes to the overall cost. Complex parts requiring more manual intervention can lead to increased labor expenses. Additionally, creating ultra-precise parts like aerospace blades might require hiring a whole team of specialty engineers to make them pass the multiple inspection requirements. Also, many filters require cleaning, which increases the labor cost.
- Yield Rates: The efficiency of material usage, measured by the casting yield, affects costs. A higher yield indicates less material waste, leading to lower costs.
How Reducing Scrap and Rework Impacts ROI
One of the biggest hidden costs in investment casting is scrap and rework. Defective castings lead to wasted materials, additional labor, and longer processing times. By improving filtration efficiency, manufacturers can significantly reduce these losses.
The True Cost of Scrap
Every defective casting contributes to unnecessary expenses, including:
- Material waste: High-value metal alloys lost due to inclusions or non-fill issues.
- Labor costs: Additional processing time for reworking flawed parts.
- Production delays: Increased cycle times and disruptions in the manufacturing process.
Reducing scrap and rework isn’t just about cutting losses—it’s about maximizing return on investment (ROI). Holy Filters are engineered to enhance filtration efficiency, improve metal alloy purity, and prevent costly defects. By achieving a higher yield, manufacturers see increased throughput without additional material or labor costs.
Case Study: Real Cost Savings
One of our aerospace clients saw yield improvements of 6-12% when switching from foam to Holy Filters, reducing scrap costs and improving overall profitability.
Achieving Cost-Effective Precision in Investment Casting
Investment casting requires balancing cost, efficiency, and precision. The right filter plays a crucial role in achieving all three. Here’s how:
- Optimizing Flow Rates
- Laminar flow prevents turbulence, reducing splashing and non-fill defects.
- Proper flow control reduces non fills by controlling the rate at which the casting is filled.
- Improving Dimensional Accuracy
- In thin walled castings maintaining a high flow rate is crucial to achieve less non fills. Holy Filters maximize flow rate while providing the best filtration.
- Precision filtration reduces the risk of voids, ensuring high-quality investment casting parts.
- Lowering Overall Processing Costs
- Fewer defects mean reduced rework, cutting down labor and material costs.
- Drop-in filters like ceramics eliminate maintenance efforts, streamlining the investment casting process.
Making the Right Investment in Filtration
Investment casting cost estimation isn't just about the initial purchase price of filters. It requires a long-term view of how filtration impacts quality, efficiency, and profitability.
At Applied Ceramics, we help manufacturers choose the right filter to meet their quality requirements while optimizing processing costs.
Interested in improving your casting process while reducing costs? Contact us today to explore how our dedicated engineers can enhance your investment casting operations.