Precision in investment casting isn’t just a goal; it’s a necessity. Industry success –ranging from...
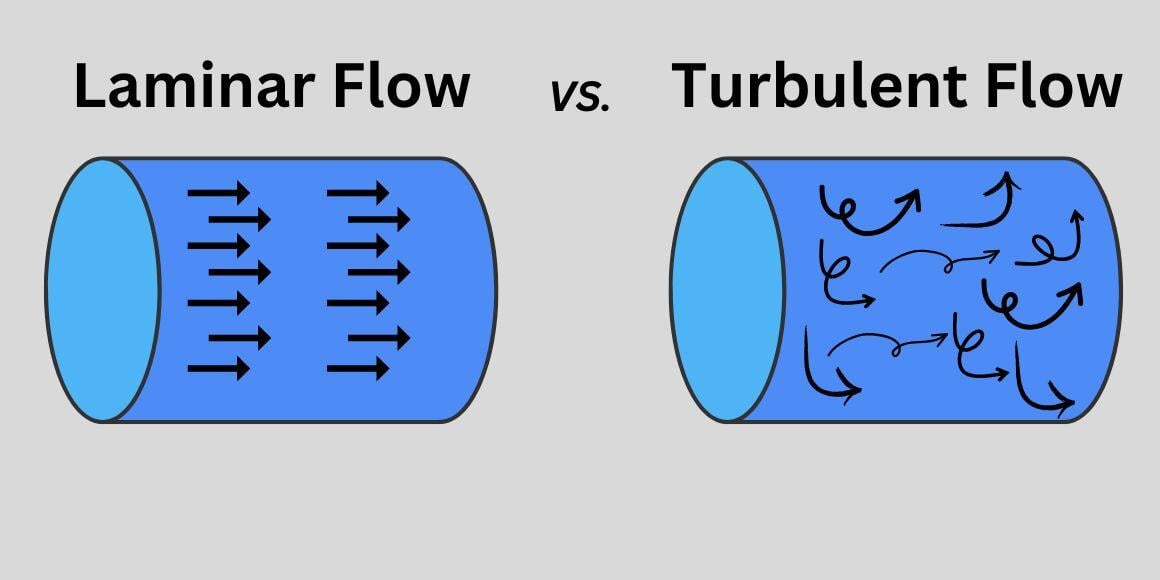
The Science Behind Laminar Flow in the Investment Casting Process
In the investment casting industry, precision is paramount. Every step in the process, from creating molds to pouring molten metal, must be executed with meticulous care to produce components that meet stringent quality standards. One often-overlooked yet critical factor in achieving these results is laminar flow—a smooth, consistent flow of molten metal that can significantly impact the investment casting process.
Let’s explore how laminar flow enhances alloy purity, improves thin-wall castings, and ensures consistent structural integrity while highlighting the role of ceramic filters in achieving this crucial flow dynamic.
The Challenge: Turbulent Flow and Its Consequences
Before delving into the benefits of laminar flow, it’s important to understand its counterpart: turbulent flow. When molten metal flows in a chaotic manner, it introduces air bubbles, inclusions, and uneven distribution of the material. This can lead to:
- Dimensional inaccuracies in the final casting.
- Increased surface defects, requiring additional rework.
- Non-fill issues, particularly in thin-wall castings.
For manufacturers producing critical components like turbine blades or intricate aerospace parts, such flaws are unacceptable. These issues compromise structural integrity and lead to increased costs and wasted materials during investment casting.
How Laminar Flow Enhances Alloy Purity During Investment Casting Process
Laminar flow, characterized by smooth and predictable movement, eliminates many of the problems associated with turbulent flow. In the investment casting process, maintaining laminar flow ensures that molten metal fills the mold uniformly, preventing air pockets, valuable metal wasted on splash, and reducing inclusions.
One key factor in achieving laminar flow is the use of ceramic filters, which promote consistent flow rates and remove impurities. Applied Ceramics’ Holy Filters, for example, feature straight-channel designs that provide 100% surface interaction, capturing slag and debris while allowing the alloy to flow uninterrupted and as fast as desired.
An improved flow dynamic results in alloys with superior purity, which is critical for components exposed to extreme conditions, such as high temperatures and intense stress.
Impact on Thin-Wall Castings and Structural Integrity
Thin-wall castings require a very high flow rate. On the other hand, these processes require molten metal to flow evenly into tight spaces without interruptions or splashing. Laminar flow ensures:
- Uniform Distribution: Laminar flow enables the molten metal to fill molds evenly and fast, preventing uneven cooling or incomplete sections (non-fills). This uniformity is crucial for maintaining the desired grain structure and ensuring the component can withstand operational stresses.
- Improved Grain Structure: Laminar flow ensures controlled cooling, critical for advanced castings like directionally solidified or single-crystal components. These precise grain orientations enhance creep resistance and mechanical strength, essential for components like turbine blades.
- Fewer Voids and Defects: By minimizing splashing and oxidation, laminar flow reduces the formation of inclusions, voids and surface defects, resulting in components with higher dimensional accuracy and better fatigue resistance.
With laminar flow, manufacturers can achieve the level of precision required for high-performance applications while reducing material waste and production delays.
Why You Should Use a Filter For Laminar Flow
In the world of investment casting, filters can be the difference between success and costly setbacks, yet their potential often goes unnoticed. Many newer engineers are unaware of a well-designed filter's profound impact, from reducing inclusions and defects to optimizing flow rates. This knowledge isn’t typically taught in school but gained through years of experience in the highly specialized, tight-knit casting industry.
It’s also important to understand that not all filters are created equal. Different materials, structures, and designs produce varying results, and the right choice depends on your specific process.
Our high-tech ceramic filters feature a unique honeycomb structure that:
- Promotes consistent flow rates, reducing turbulence.
- Improves filtration efficiency, allowing filtration to be sped up where it’s needed or slowed down if the process requires it.
Applied Ceramics’ filters have a particular feature that sets them aside: they turn filtration into a density problem instead of a capturing problem. Dross is the oxide form of alloy, which adheres to our ceramic filters. This reduces scrap and rework by capturing the dross and other foreign contaminants. By integrating these filters into their investment casting processes, manufacturers can achieve higher yields, lower scrap rates, and superior overall quality.
Bobby Mitchell, Applied Ceramic’s CEO talks about the benefits of using an AC filter:
Laminar Flow: A Competitive Advantage
In an industry where precision defines success, laminar flow offers a competitive edge. By optimizing alloy purity, improving thin-wall castings, and enhancing structural integrity, it directly contributes to higher-quality components and cost savings. Manufacturers who prioritize flow dynamics in their investment casting processes can expect:
- Improved yields, with fewer defects and less rework.
- Increased customer satisfaction, thanks to reliable, high-quality components.
- Enhanced operational efficiency, reducing downtime and material waste.
Redefining Investment Casting with Laminar Flow
Laminar flow isn’t just a scientific concept—it’s a game-changer for the investment casting industry. By embracing the right ceramic filters, manufacturers can overcome the challenges of turbulent flow and unlock new levels of precision and efficiency.
At Applied Ceramics, we take the guesswork out of filter selection. Our team works closely with you to identify the best filter for your process and ensure seamless integration into your operations. The result? Higher-quality castings, faster production cycles, and significant cost savings—all tailored to your unique needs.
Ready to improve your casting process with laminar flow?
Contact Applied Ceramics today to learn more about our advanced ceramic filters and how they can transform your production capabilities.