Investment casting is a precise and cost-sensitive process where every variable—from metal alloy...
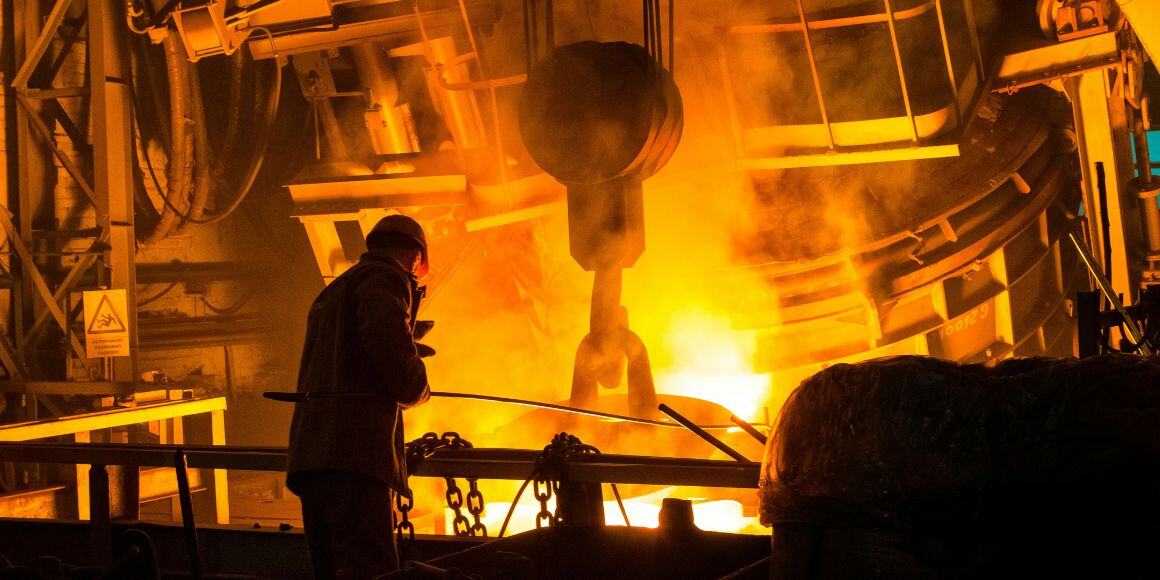
Choosing the Right Filter for Your Investment Casting Process
Precision in investment casting isn’t just a goal; it’s a necessity. Industry success –ranging from aerospace to automotive– hinges on producing flawless, high-performance components. Amid the countless variables that influence casting quality, one often-overlooked factor can make all the difference: the molten metal filter.
In this guide, we’ll explore how to choose the ideal molten metal filter for your investment casting process.
Why molten metal filters are essential
Molten metal filters pose many benefits for the investment casting process. They can help control the alloy flow to speed it up, avoiding inclusions. On the other hand, they can help slow the flow to allow more complex processes like directionally solidified castings. Ultimately, the right filter can ensure cleaner metal and fewer defects.
The stakes are even higher for industries like aerospace, where safety and quality are paramount. Engineers are responsible for maintaining production standards and could face personal liability under laws like the Wendell H. Ford Aviation and Investment Act if defective parts lead to aerial accidents.
Beyond safety concerns, ceramic casting filters help reduce the frequency of reworks, optimize laminar flow, and prevent non-fills. These benefits collectively enhance the efficiency and cost-effectiveness of the investment casting process.
common misconceptions about molten metal filters
Despite their importance, misconceptions about molten metal filters abound. Some engineers mistakenly believe filters are unnecessary if their initial runs appear successful. Others fail to account for how filters’ performance impacts long-term consistency in high-temperature environments. Here are two key myths debunked:
- “Filters are optional.” While skipping filters might work in low-stakes scenarios, industries like aerospace and automotive demand consistent, high-quality results that filters help ensure by increasing filtering speed or controlling the flow to enhance productivity.
- “All filters are the same.” In reality, filters vary in material, size, shape, placement, and performance, making it crucial to tailor your choice to your specific needs.
factors to consider when choosing a molten metal filter
Selecting the right filter involves evaluating several critical factors:
1. Your Application Goals
- Are you looking to achieve higher flow rates without getting air into your alloy or lose thousands of dollars with the splashing?
- Do you need laminar flow for smoother casting or something else entirely?
The way you answer these questions will determine the shape, material, and placement of your filter.
2. Filter Placement
- Filters placed closer to the true casting improve flow smoothness and reduce non-fills.
- Cup filters, located farther from the mold, are better for achieving high flow rates.
3. Material Compatibility
- The choice of material for your filter depends on casting temperatures and alloys. For example:
- Magnesium Stablized Zirconia for extreme Thermal shock resistance.
- Zirconia-Mullite or pure Alumina for moderate to high temperatures. (Our team can help you choose the best option for your process, considering zirconia-mullite and alumina prices can vary).
- Mullite for High temperatures and intermediate thermal shock resistance.
honeycomb vs. foam filters
Understanding the differences between filters can help you make an informed decision. Here’s a quick comparison between regular ceramic foam filters and Applied Ceramics unique Honeycomb design:
Feature |
Applied Ceramics Honeycomb Filters |
Foam Filters |
Filtration Speed |
Starting at 1000 mL / Sec of alloy |
Starting at 600 mL / Sec of alloy |
Output Purity |
Minimal debris |
Potential debris |
Maintenance |
No cleaning required |
Cleaning may be needed |
advice for new investment casting plants
After over 50 years of working in the investment casting industry, we've encountered multiple problems that stop our customers from getting the best results. With this experience in mind, here are a few tips if you're thinking about starting a new metal foundry facility:
- Collaborate with Experts: Work with experienced engineers to design a layout that supports flexibility and future expansion. The investment casting industry is a niche with its own troubles, needs, and movements. Only a seasoned expert will know how to avoid future issues.
- Prioritize Testing: Although expertise is key, you should not rely on assumptions. Test different filters and configurations to find what works best.
- Focus on Longevity: Don’t waste time and money “saving” on equipment. Invest in durable equipment and materials to reduce long-term costs.
custom filters vs. standard options
In high-stakes industries, custom filters offer solutions for unique casting challenges. Depending on the process, filters need to fit specific mold shapes and sizes. Custom filters can:
- Optimize placement for enhanced flow and purity.
- Handle varying alloys and temperatures with ease.
- Provide a better process efficiency compared to standard options.
Applied Ceramics specializes in developing custom molten metal filters to meet the unique demands of diverse industries. These filters are rigorously tested to ensure compatibility and reliability across a wide range of casting environments.
ready to cast success into perfection?
Choosing the right molten metal filter is a critical step in optimizing your investment casting process. From understanding your application goals to selecting the right materials and configurations, a thoughtful approach can significantly enhance casting quality and operational efficiency.
For tailored advice, sample filters, and expert guidance, reach out to Applied Ceramics. Let us help you achieve precision and reliability in your next casting project.